About flow chemistry
Learn more about the basics of flow chemistry
Find answers for the most common questions about flow chemistry:
Do you prefer to learn more in a video?
Watch our Flow Chemistry Basics I. webinar which summarizes the basic principles you will need to perform flow chemistry experiments. Learn about basic reaction parameters like residence time, flow rate, temperature, and pressure, as well as the most fundamental characteristics of flow chemistry and how it compares to batch technologies. Also, you can learn about the basic instruments that will allow you to perform simple flow experiments.
What is flow chemistry?
About flow chemistry
Flow chemistry has become a valuable tool for synthetic chemistry. It involves conducting reactions in the continuous flow of the reagents or their solvents. Although chemical industry has been utilizing the concept for some time, modern flow chemistry revolutionized laboratory-scale synthesis in the early 2000s. With the advent of smaller, laboratory-sized instruments, it became possible to transform small quantities of materials in a highly controlled and efficient manner.
One of the key advantages of continuous flow technology is the expanded parameter window it offers for chemical synthesis. It allows for a wider range of temperatures and pressures, as well as new possibilities for reaction mechanisms, potentially leading to the creation of novel molecules. Furthermore, flow chemistry facilitates the precise control of reaction conditions, enabling fine-tuning of reaction selectivity. Moreover, it enhances safety by providing a means to handle hazardous or corrosive reagents and perform potentially dangerous reactions in a significantly safer manner.
Nowadays, flow chemistry continues to gain momentum as an emerging trend within the scientific community. More and more academic and industrial research groups are utilizing flow technology to explore and access new compounds. This growing interest is paving the way for the adapting this on a production scale, particularly in the pharmaceutical industry. Notably, the FDA's guidelines encouraging the transition from batch to continuous production further support the adoption of flow technology. As this trend continues to evolve, flow chemistry holds the potential to revolutionize the synthesis of complex compounds and streamline manufacturing processes, unlocking new possibilities in the field of chemistry.
Flow rate and residence time
Residence time refers to the duration that each portion of the reaction mixture spends in the continuous flow reactor. It can be determined by dividing the volume of the reactor by the flow rate of the reaction mixture. The formula for calculating residence time is as follows:
Residence time = Volume of the reactor / Flow rate
By adjusting either the volume of the reactor or the flow rate, the residence time can be precisely controlled. This allows for fine-tuning of the reaction conditions. In situations involving multiple liquid inlet lines, the flow rates of the compounds are combined, and the residence time should be calculated using the total flow rate.
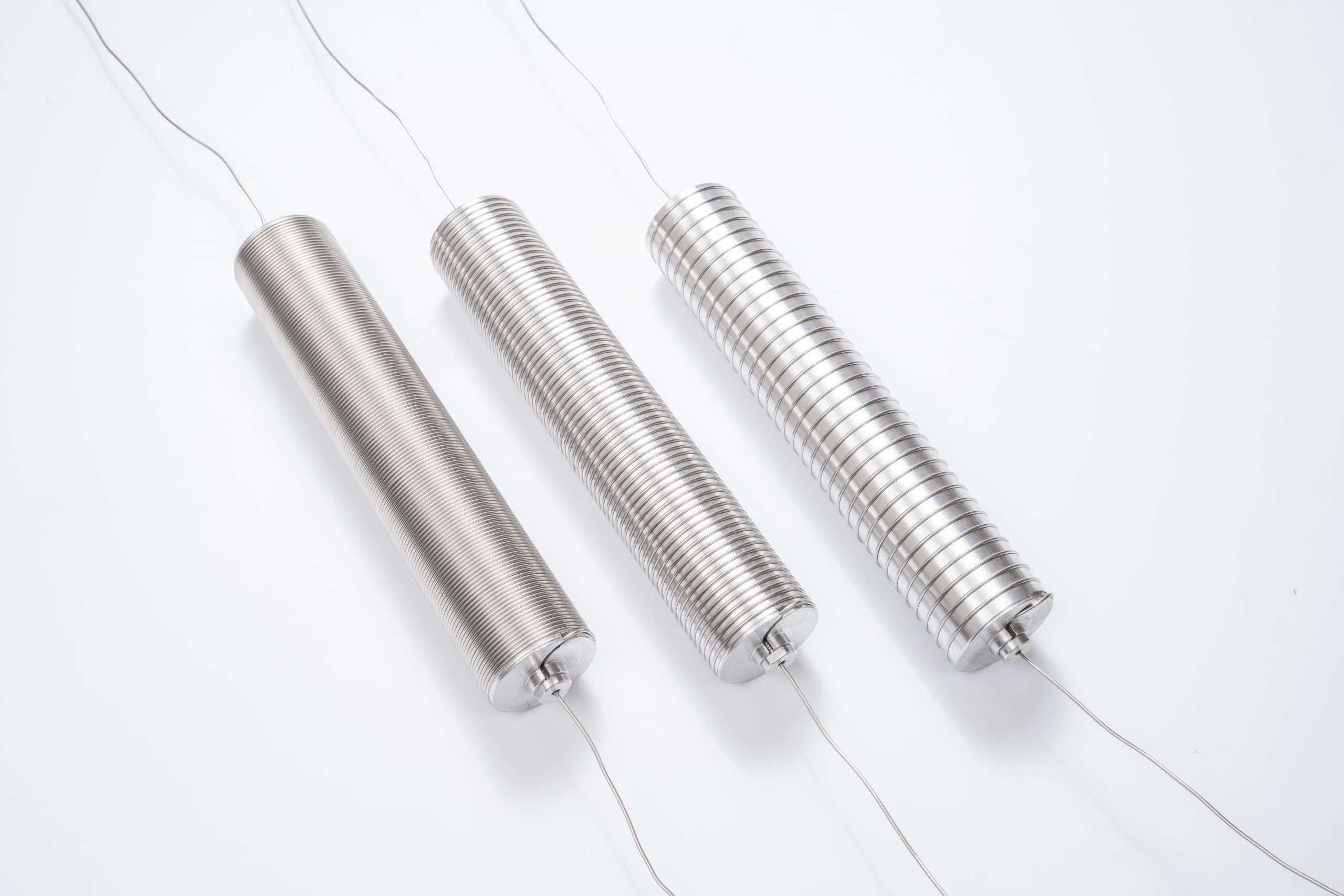
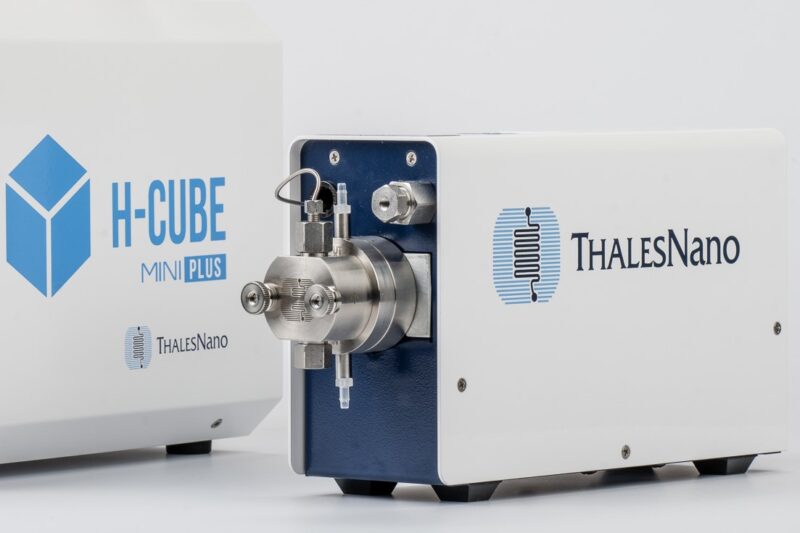
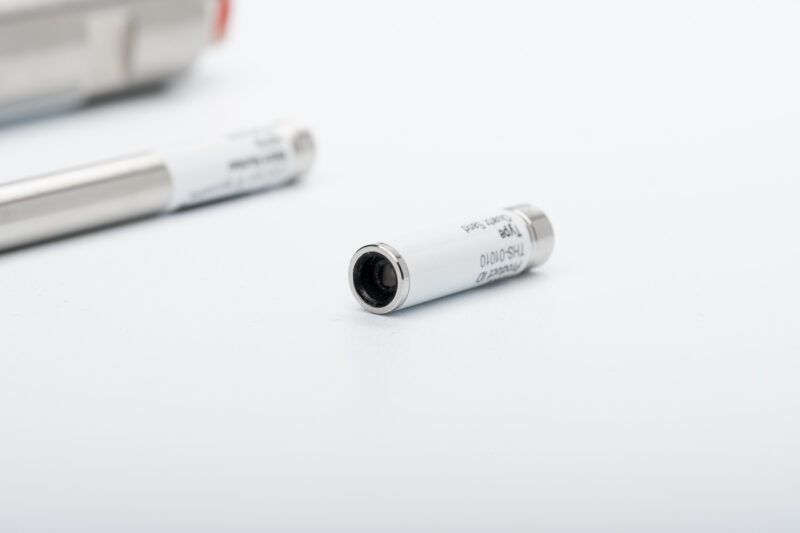

What are the advantages of flow chemistry?
Safety
Flow chemistry offers significant improvements in safety for both the user and the chemical process through various means:
- Separate handling of reagents: Ability to handle reagents individually, even under inert atmospheres, reducing the potential for accidents or unwanted reactions.
- Minimal reagent and product loss: Relatively small reactor volumes help minimize the loss of reagents or products in the event of unexpected events, ensuring safer operation.
- Easy quenching of reactions: Flow chemistry enables quick and efficient quenching of reactions, allowing for the effective elimination of reactive intermediates and by-products, which contributes to overall process safety.
- Continuous work-up of products: Seamless integration of the desired product's work-up into the continuous flow, ensuring a continuous and controlled process with reduced handling and associated risks.
- Minimal user exposure: Due to the closed system, the user's exposure to chemicals is minimized, further enhancing safety measures.
Heat transfer and temperature control
In traditional batch reactions, mixing often results in turbulent flow, which can lead to uneven heat transfer and temperature gradients. However, in flow chemistry, the geometry and small inner diameter of the reactor channels promote laminar flow and radial diffusion (Re < 2500). As a result, flow chemistry enables rapid and efficient mixing to occur before the reaction mixture enters the reactor. This controlled mixing allows for improved heat transfer and temperature homogeneity throughout the reaction process.
One key advantage of continuous flow reactors is the precise temperature control offered by continuous flow instruments. With continuous flow systems, temperature regulation can be finely tuned, allowing for optimal reaction conditions. Additionally, the exceptionally large surface-to-volume ratio of microreactors in flow chemistry enhances heat transfer efficiency.
The combination of precise temperature control and efficient heat transfer enables the control of reaction mechanisms and selectivity in flow chemistry. By maintaining consistent and controlled temperatures, the desired reaction pathway can be favored, leading to improved control over the outcome of the reaction.
Faster reactions
Flow chemistry technology expands the chemical parameter window, enabling the application of higher pressure and temperature compared to traditional batch chemistry. In flow systems, it is possible to subject solvents to elevated pressure, allowing them to be heated well above their boiling points while remaining in the liquid phase.
The increased pressure and temperature in flow chemistry have a direct impact on reaction kinetics. According to the Arrhenius equation, higher temperatures result in decreased reaction times. By operating at elevated temperatures, flow chemistry enables faster reactions due to the enhanced kinetic energy of the reactant molecules.
The ability to utilize higher pressure and temperature in flow chemistry accelerates reaction rates, leading to significantly reduced reaction times compared to traditional batch methods. This advantage opens up new possibilities for efficient synthesis and rapid production of the desired compounds.
Controlled reactions
Continuous flow instruments offer efficient regulation and monitoring capabilities for various aspects of the reaction, including the stoichiometry, residence time, temperature, and pressure. This precise control allows for the manipulation of reaction mechanisms and the fine-tuning of selectivity, enabling access to desired products.
One of the notable advantages of flow chemistry is the ability to rapidly and easily adjust reaction conditions. With continuous flow systems, changes in parameters such as temperature and residence time can be made quickly, facilitating optimization and exploration of reaction conditions.
Furthermore, the use of small reaction mixture volumes in flow chemistry enables the efficient identification of optimal parameters for a given chemical transformation. This streamlined process significantly reduces the amount of starting materials required, allowing for faster experimentation and discovery of ideal reaction conditions.
In addition, several commercially available flow chemical systems offer automation capabilities, simplifying the optimization processes. Automation enables the systematic exploration of reaction parameters, making it easier to identify optimal conditions for improved yields and desired products.
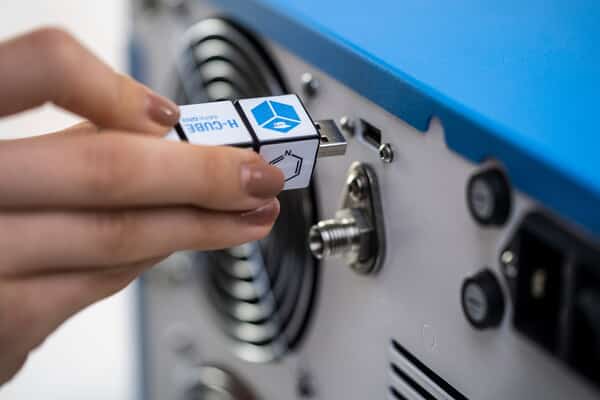


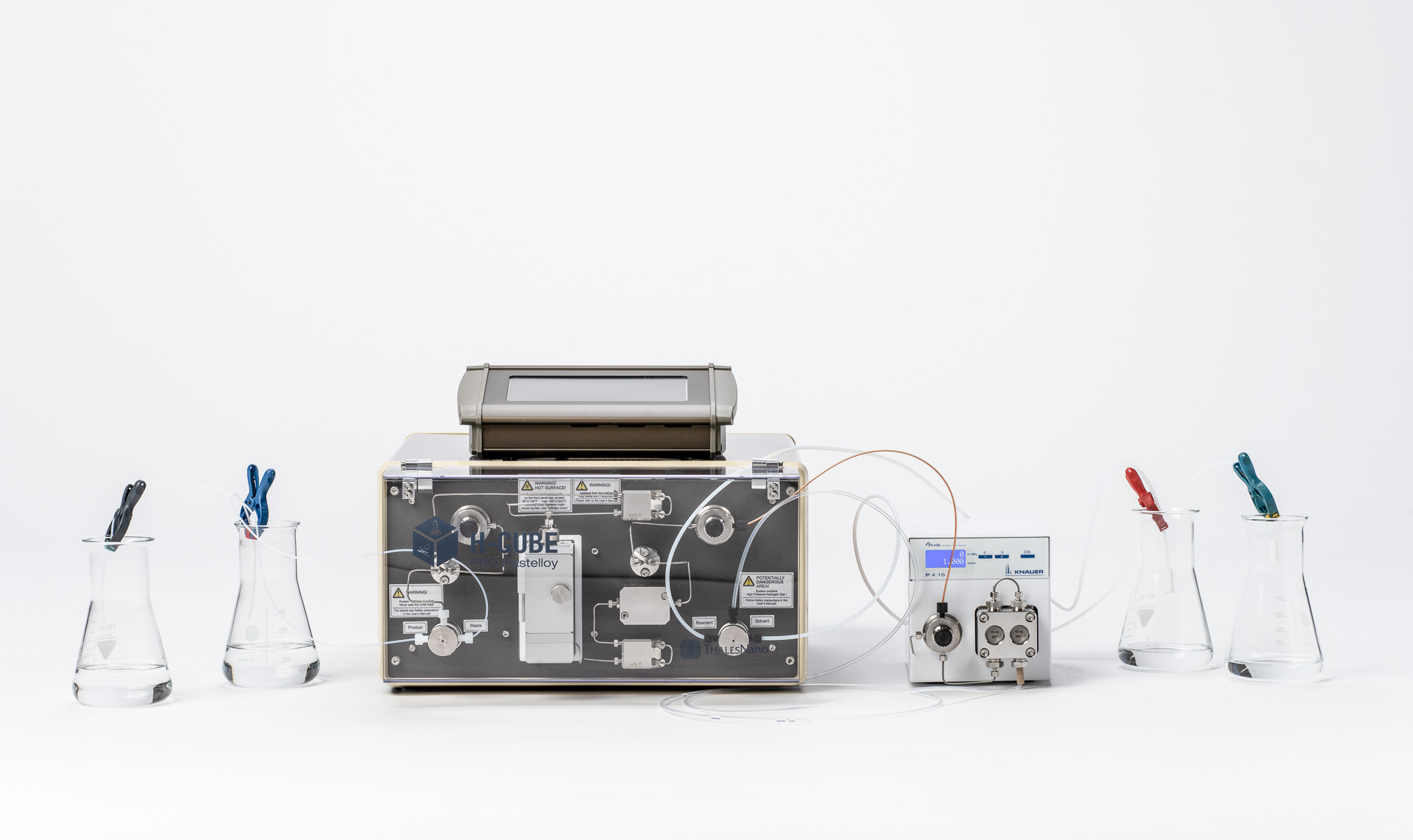
How to perform continuous flow reactions?
What do you need for flow reactions?
This section provides insights into the essential equipment and accessories required for setting up a basic flow chemistry system. You will discover the necessary components needed to perform various types of flow reactions, including gas/liquid or gas/liquid/solid phase reactions. Gain a comprehensive understanding of the foundational elements required to embark on your journey into the world of flow chemistry.
Pumps
For laboratory-scale continuous flow experiments, only a few mechanical pumps are suitable. Among the diverse range of commercially available options, two main groups stand out: syringe pumps and piston pumps.
Syringe pumps are renowned for their accuracy and pulsation-free dosing capabilities. The syringe itself can be crafted from various materials such as polymers, glass, or stainless steel, offering flexibility and compatibility. The flow rates achievable with syringe pumps are dependent on the volume of the syringe employed.
On the other hand, piston pumps generate a slightly pulsating flow pattern. These pumps excel at handling high pressures, and are capable of reaching pressures up to 100-400 bar. Different-sized pump heads, often featuring stainless steel or ceramic inlays, contribute to their versatility and durability.
Mixers
When it comes to mixers in flow chemistry, various designs and techniques are employed to achieve efficient mixing. The commonly used approaches:
- Diffusion mixers: These mixers maintain laminar flow conditions to promote gentle mixing. They can be implemented by extending the tube length or dividing the flow into multiple laminates, thereby increasing the interfacial area between fluidic layers.
- Convective diffusion enhancement: This technique involves inducing a turbulent flow regime to deform the lamellar arrangements, resulting in more thorough mixing. By promoting convective diffusion, these mixers enhance the overall mixing efficiency.
- Static mixers: Particularly useful in large-scale reactions, static mixers utilize tube inserts, such as blades/helices or fluid stretching, to generate turbulence and intense radial mixing. This ensures effective blending of the fluids and enhances mixing performance.
By employing a range of mixer designs and techniques, flow chemistry enables precise control and optimization of the mixing process, contributing to improved reaction outcomes.
Reactors
When it comes to reactors in flow chemistry, different types and materials are recommended based on the nature of the reaction:
For homogeneous reactions:
- Coils or loops are commonly recommended for their versatility.
- These reactors can be constructed from various materials such as polymers (PTFE, PEEK, FEP, PFA), stainless steel, or alloys like Hastelloy.
- Consider the chemical resistance, temperature tolerance, and pressure limits of the reactor material to ensure a successful experiment without any issues.
- Due to their relatively high surface-to-volume ratio, these reactors offer fast mixing and efficient heat transfer.
- Glass or stainless steel chip reactors are available for small-scale reactions and optimization processes, often equipped with special mixer and preheater zones.
- Microreactors typically have reactor channel diameters ranging from 100 to 500 µm and can feature multiple liquid input lines.
For heterogeneous reactions:
- Columns and packed bed reactors are recommended for the application of solid reagents.
- These reactors are commonly made of glass, various polymers, or stainless steel.
- They are available pre-filled with selected reagents or catalysts or can be purchased empty, allowing users to fill them with their own materials.
Heaters and coolers
Heating or cooling the reaction mixture is often necessary, depending on the specific chemical application. One straightforward solution is to immerse the reactor (such as a tube, chip, or packed column) in a cooling or heating bath. However, with the advancements in continuous flow technology, precise and well-controlled heater and cooler instruments have emerged, enabling chemists to regulate and monitor reactions that are sensitive to temperature changes while maintaining control over selectivity.
In today's landscape, a variety of continuous flow heater and cooler units are readily available on the market, either as part of a comprehensive system or as standalone modules. When selecting the most suitable instrument for a given synthesis, factors such as the reaction scale, the required maximum and/or minimum temperature, the number of reagents involved, and the planned residence time should all be taken into consideration.
The availability of these advanced heater and cooler instruments empowers chemists to perform routine laboratory syntheses with greater precision and control, facilitating the exploration of temperature-dependent reactions and fine-tuning reaction selectivity.
Mass flow controllers (MFCs)
Mass flow controllers (MFCs) play a crucial role in flow chemistry by facilitating the precise introduction of gases into the liquid line. These controllers are specifically designed to regulate and control the amount and flow rate of gases in the system.
Back-pressure regulators (BPRs)
Back-pressure regulators (BPRs) play a vital role in flow chemistry by maintaining a specified upstream pressure. They are particularly important for gas-liquid reactions, where precise pressure control is essential.
In flow chemistry, applying higher back-pressure with the help of BPRs helps to keep solvents and reactants in the liquid phase, even when they would normally boil at the operating temperature. This is achieved by increasing the boiling points of the liquids, allowing for reactions to occur under controlled liquid conditions.
BPRs are commonly constructed from polymers or stainless steel, ensuring compatibility with a wide range of chemical systems. Various types of BPRs are available, including static BPRs with pre-set pressure values and adjustable BPRs that allow for variable pressures within a specific pressure range.
Other accessories
Fittings and tubing: Fittings and tubing are used to connect different parts of the system into a continuous reaction line. They are available in various materials, such as polymers (PTFE, PFA, PEEK, etc.) or stainless steel. When planning a reaction, it is important to consider the chemical and mechanical resistance, as well as the temperature and pressure tolerance of the chosen materials.
Product Collection: In flow chemistry, manual or automated product collection methods can be employed. There are several automated product collector modules available in the market, offering convenient and efficient collection of reaction products. Product lines can be further connected to various work-up and analytical methods for downstream processing and analysis.

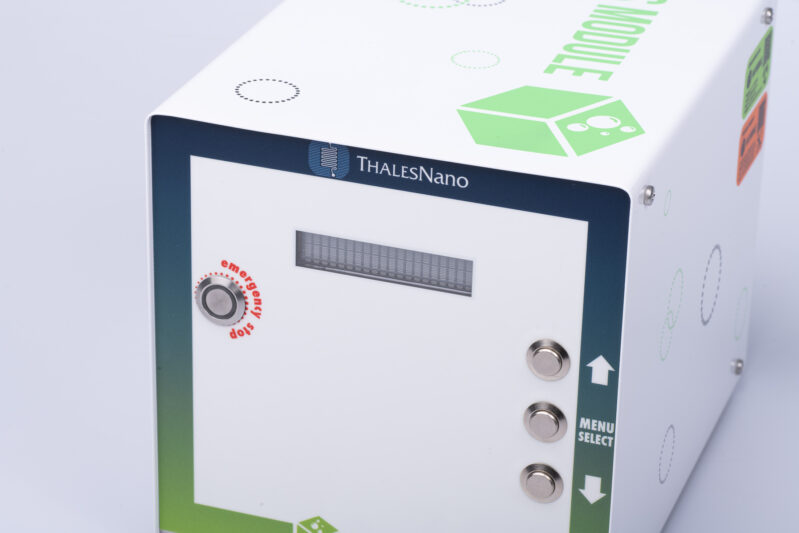

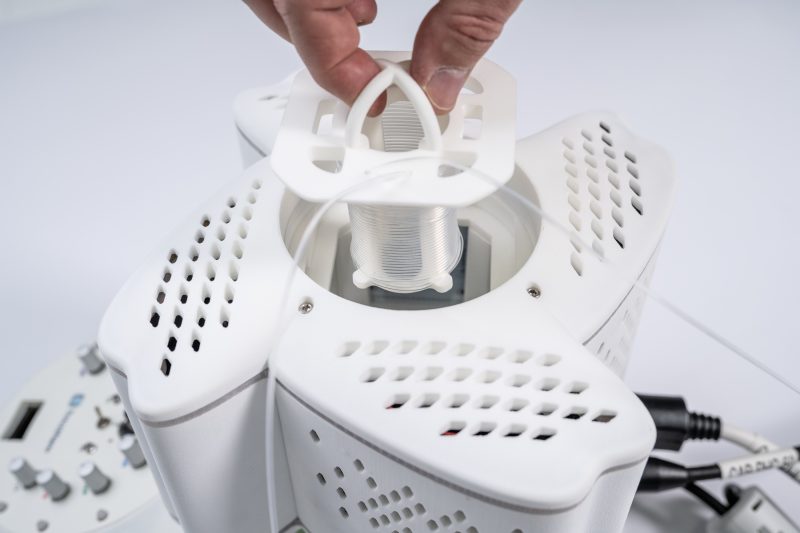
How to design flow experiments?
What aspects to consider when planning flow reactions?
Before entering the laboratory, it is essential to consider several important aspects of flow reactions to achieve maximum efficiency, enhance safety, and minimize reaction times. These aspects include selecting the appropriate solvent or solvents for the planned chemical transformation, exploring the role of pre-mixing (whether it should be avoided or exploited), careful planning of reaction conditions such as temperature, pressure, residence time, etc., choosing suitable analytical methods if necessary, and devising strategies for work-up and purification processes. By addressing these aspects, researchers can optimize their flow chemistry experiments and pave the way for successful implementation.
Solvents
The careful selection of solvent(s) has a significant impact on the entire process:
- Consider the solubility of all components (reagents, products, side-products, and additives) in the chosen solvent. If necessary, conduct tests to gather more information about the reaction.
- For multistep synthesis and solvent change, if possible, use a single solvent throughout the entire process. This helps maintain consistency and simplifies the workflow.
- Solvents with lower boiling points can be utilized, even when subjected to higher back-pressure. This facilitates easier work-up procedures.
- Take into account the volatility of the solvents. In heterogeneous flow reactions involving gases, high gas flow rates can lead to solvent evaporation, causing precipitation of reagents and/or products and potential clogging issues.
- Solvent mixtures can be employed as an alternative solution when facing solubility problems.
- Consider the compatibility of the chosen solvent with the reactor material to avoid any adverse reactions or compatibility issues.
- It is worth noting that neat reactions, which involve performing reactions without solvents, can also be implemented when applicable.
Pre-mixing of reagents
Pre-mixing of reagents can be important in flow reactions as it can significantly influence the outcome of the reaction:
- Avoid undesired reactions in the storage flask: When conducting room temperature reactions where the starting materials are prone to react with each other, we highly recommend to store and dose the reagents separately. This approach ensures the reproducibility of the reaction and minimizes the occurrence of unwanted side reactions.
- Simplify the process when possible: In cases where a high activation energy is required for the reaction, pre-mixing the reagents and adding them simultaneously using a single starting solution can streamline the overall process. This approach can simplify the handling and improve the efficiency of the reaction.
- Exploit reactions in the storage flask: Some reaction steps, such as deprotonation, can occur before the initial transformation, which may involve heating or cooling. These steps can be implemented in the storage flask itself or by incorporating mixer units or coil reactors for effective mixing, allowing for the desired reactions to take place prior to entering the main flow reactor.
By carefully considering the pre-mixing strategy, researchers can optimize the reaction conditions and enhance the control and efficiency of their flow chemistry processes.
Reaction conditions
Continuous flow systems provide accurate temperature and pressure control over a wider range of chemical parameters than in traditional batch chemistry, which significantly affects:
- the reaction time,
- the selectivity, and
- the yield of a given chemical transformation.
In most cases, increasing the reaction temperature and/or pressure will accelerate the reaction, but the heat sensitivity of the reagents and the products formed must also be considered in order to optimize the synthetic process.
Some modules and systems use different built-in algorithms to help optimize chemical reactions faster, with minimal reaction mixture volumes.
Analytical methods
In situ analytical instruments which can be introduced directly to the liquid stream (in-line) or which use representative amounts of the reaction mixture (on-line), can provide continuous monitoring of the reaction:
- FT-IR, Raman instruments
- NMR spectroscopy devices
- MS, and
- HPLC instruments are available on the market
Using in situ analysis in continuous flow:
- Gives information about the concentration of all components of the reaction mixture.
- Short-lived intermediates can be monitored accurately.
- Gives better understanding of the reaction mechanism.
Work-up and purification
Several different in-line work-up and purification methods are available, among others:
- Continuous filtration can remove any solid impurities.
- To eliminate excess reagents or reactive intermediates, a column filled with an appropriate scavenger resin can be added into the liquid stream.
- The same method, using a suitable desiccant, is excellent for removing any traces of water before the reaction, during the addition of gases, or in the case of multistep syntheses, after the reaction and before the next reaction step.
- Liquid-liquid extraction is easily accomplished by the introduction of an additional liquid phase immiscible with the solvent used, and a membrane separator unit. Some separators are also suitable for gas-liquid mixtures to remove the gas phase.
Adding these methods to flow chemical processes is a big step towards fully automated syntheses and industrial-scale continuous flow production.
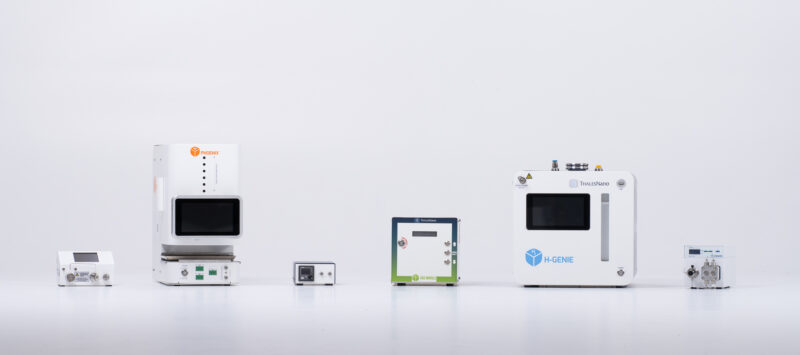
Further reading
Flow Chemistry Vol. 1: Fundamentals
Darvas, F.; Dorman, G.; Hessel, V.; De Gruyter, 2021
Chemical Synthesis in Microreactors
Schwalbe, T. et al.; CHIMIA 2002, 56(11), 636-646
The route from problem to solution in multistep continuous flow synthesis of pharmaceutical compounds
Bana, P. et al.; Bioorg. Med. Chem. 2017, 25, 6180-6189
Sign up for our Newsletter for More Information
Do you have questions?
Reach out to us at any time and experience fast and efficient support tailored to your specific needs.