Phoenix Flow Reactor
Versatile and powerful flow reactor
Flow reactor designed for high-temperature/high-pressure reactions
The Phoenix Flow Reactor is designed for high temperature/high-pressure reactions. The device enables novel compound synthesis in a parameter space not achievable with standard laboratory equipment. Given the extended parameter window (temperature up to 450°C, pressure up to 200 bar), it offers unparalleled versatility for both homogeneous and heterogeneous chemistry. Building on the advantages of the flow chemistry technology, this system makes chemical processes significantly safer.
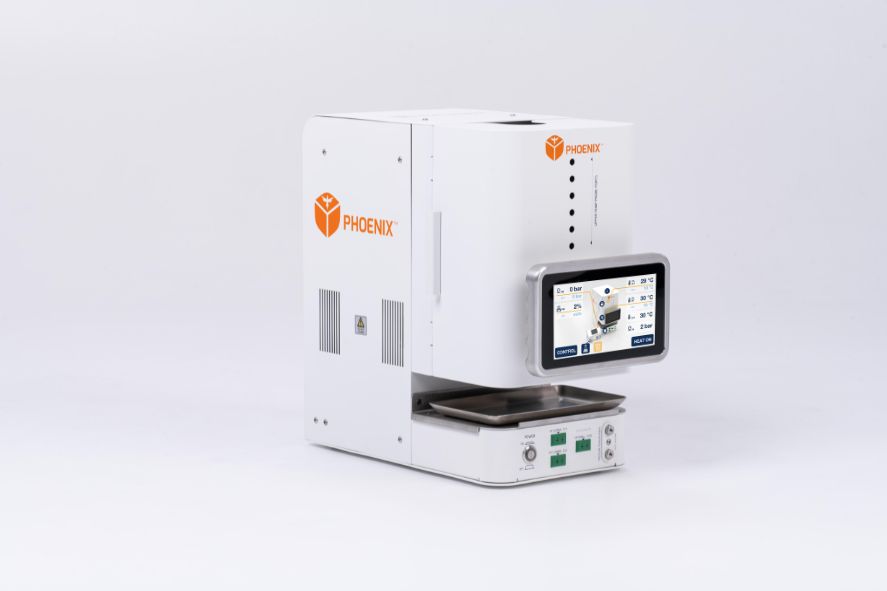

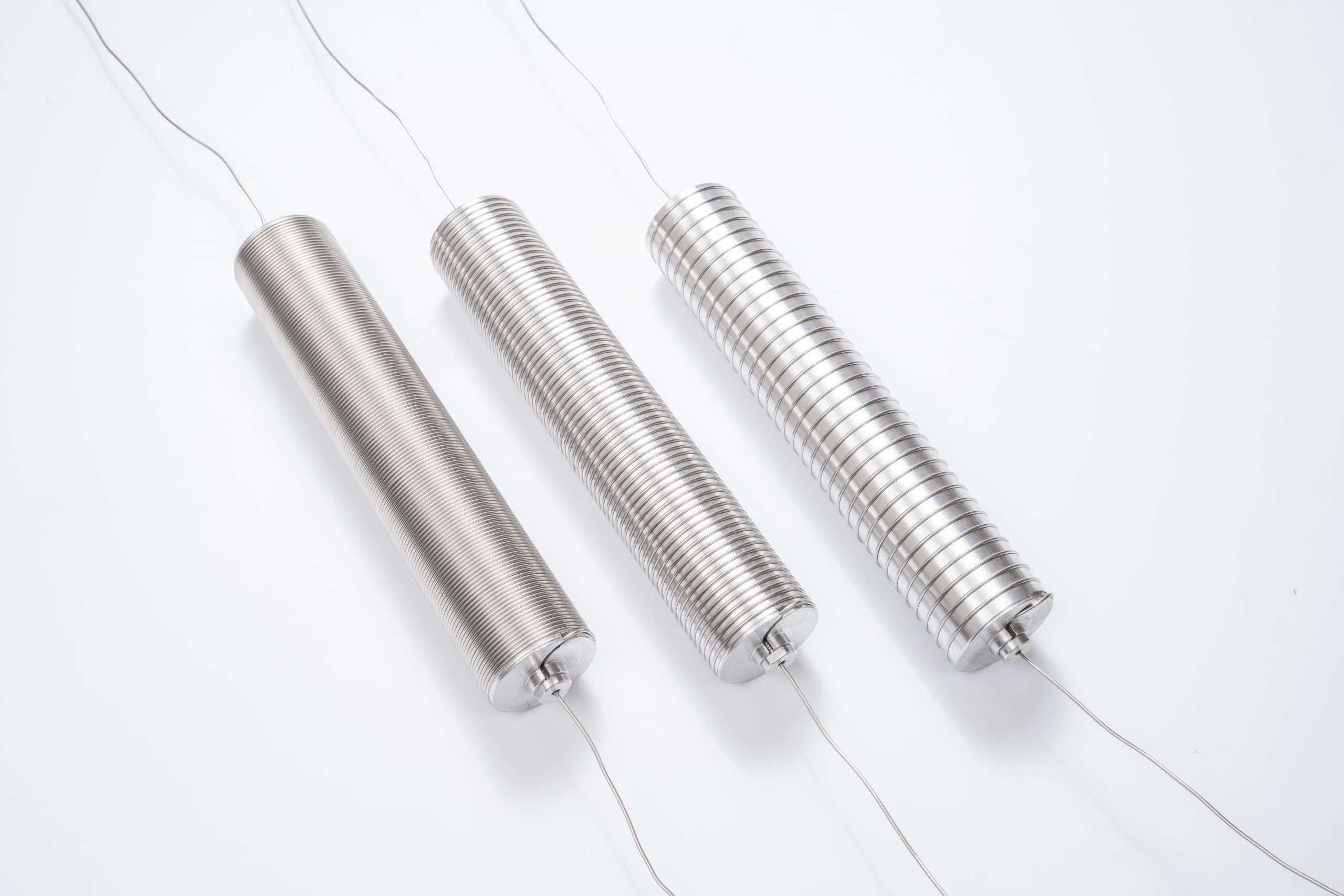
Features of the Phoenix Flow Reactor
Extended chemical parameter window: One of the most important advantages is the extended chemical parameter window of the device. With temperatures up to 450°C and pressures up to 200 bar, this reactor provides you with unprecedented control over your reactions.
Heterogeneous and homogeneous capabilities: The Phoenix Flow Reactor can be used for both heterogeneous and homogeneous reactions, allowing chemists to tackle various applications. Whether you are working with solid materials and catalysts, or are conducting homogeneous reactions, this system accommodates your needs with ease.
Simple interchange of heated elements: The Phoenix Flow Reactor offers a wide range of heated elements to suit different requirements. You can use PTFE, Hastelloy, or stainless-steel coiled loop reactors of different volumes for homogeneous reactions. Moreover, user-fillable metal-metal sealed cartridges are available to perform heterogeneous chemistry. CatCarts and MidiCarts ensure convenient and efficient catalyst testing.
User-friendly software interface and movable touch screen: The software of the Phoenix Flow Reactor allows seamless control and monitoring of the reactor parameters. With a movable GUI touch screen, you have the freedom to position the interface wherever it is most convenient for you.
Modularity: The modular design of the Phoenix flow systems enables easy integration with a wide range of instruments, allowing you to build and customize the system to your needs.
Rapid heating: Heating times are significantly reduced, enabling quicker access to the desired temperature for your reactions. In addition, the inclusion of cooling functionality ensures rapid cool-down at the end of the reaction.
Multiple temperature sensors: The reactor gives you the option to monitor temperature with the help of multiple temperature sensors throughout the system, enabling accurate and reliable data acquisition.
Modules for the Phoenix Flow Reactor
THS System Controller® >>
Enables communication between all connected devices within the fleet. Its software counterpart, THS ReAction® Software, allows for precise operation of the entire fleet from a single screen.
THS RS232-CAN Converter
Designed to connect external modules, such as HPLC pumps, mass flow controllers, and autosamplers to the fleet through the THS System Controller.
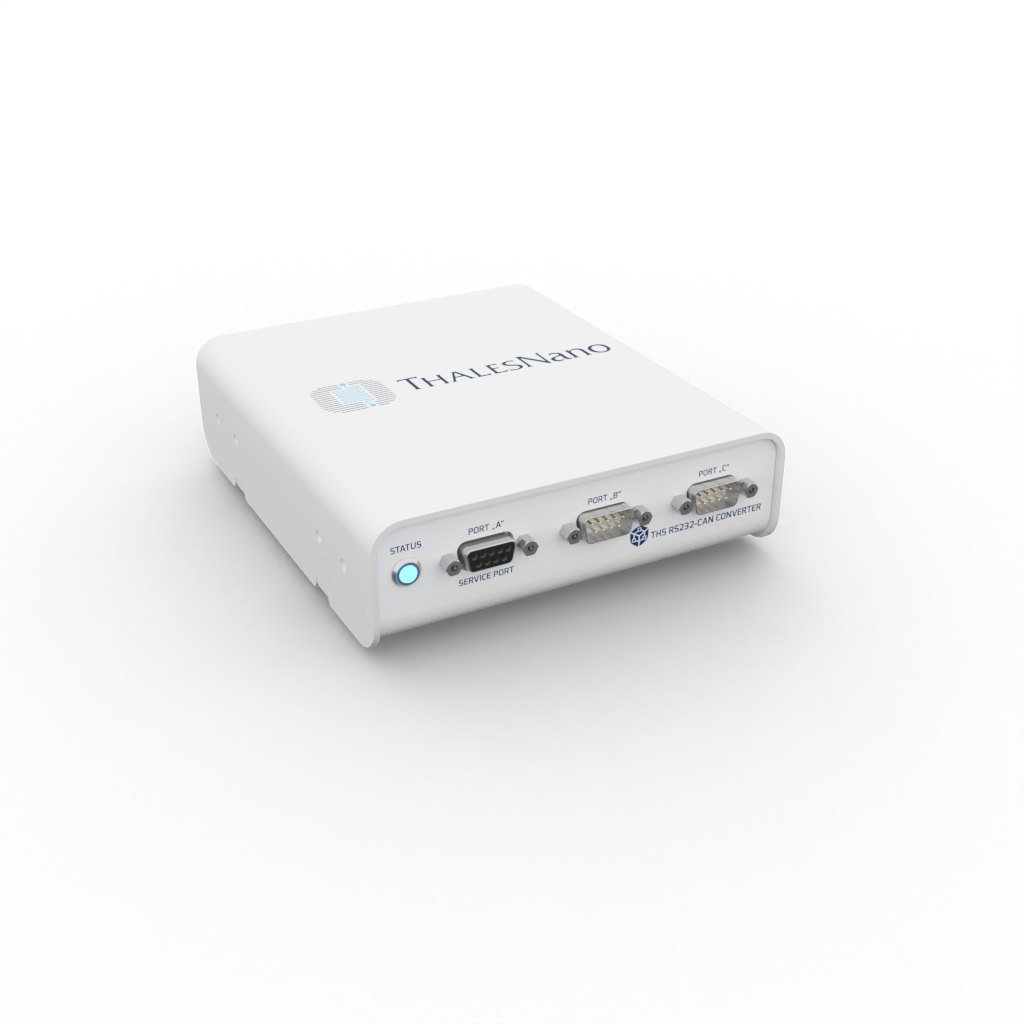
H-Genie® >>
On-demand, high pressure (up to 100 bar) hydrogen generator, producing 99.99% (4.0) pure hydrogen gas via water electrolysis, with flow rates up to 1NL/min.
H-Genie® Lite >>
On-demand, high pressure (up to 50 bar) hydrogen generator, producing 99.9% (3.0) pure hydrogen gas via water electrolysis.
Gas Module / Gas Module Plus >>
Designed for the precise dosing of 14 different gases at flow rates up to 1NL/min and up to 100 bar pressure.
Reactor Module >>
High-temperature, high-pressure reactor unit for catalyst testing, catalyst screening, and multi-step reactions.
Pressure Module 2 >>
New generation motorized back pressure regulator with a built-in pressure sensor. System pressure can be set up to 200 bar and pressure levels can be seamlessly monitored.
Mixer Module >>
High-performance static mixer for gas-liquid mixtures. Operates up to 200 bar and supports a wide variety of gases and liquids.
ThalesNano Micro HPLC pump
3 mL/min or 10 mL/min capacity pumps with built-in inlet pressure sensors, maintaining a constant flow within the system.
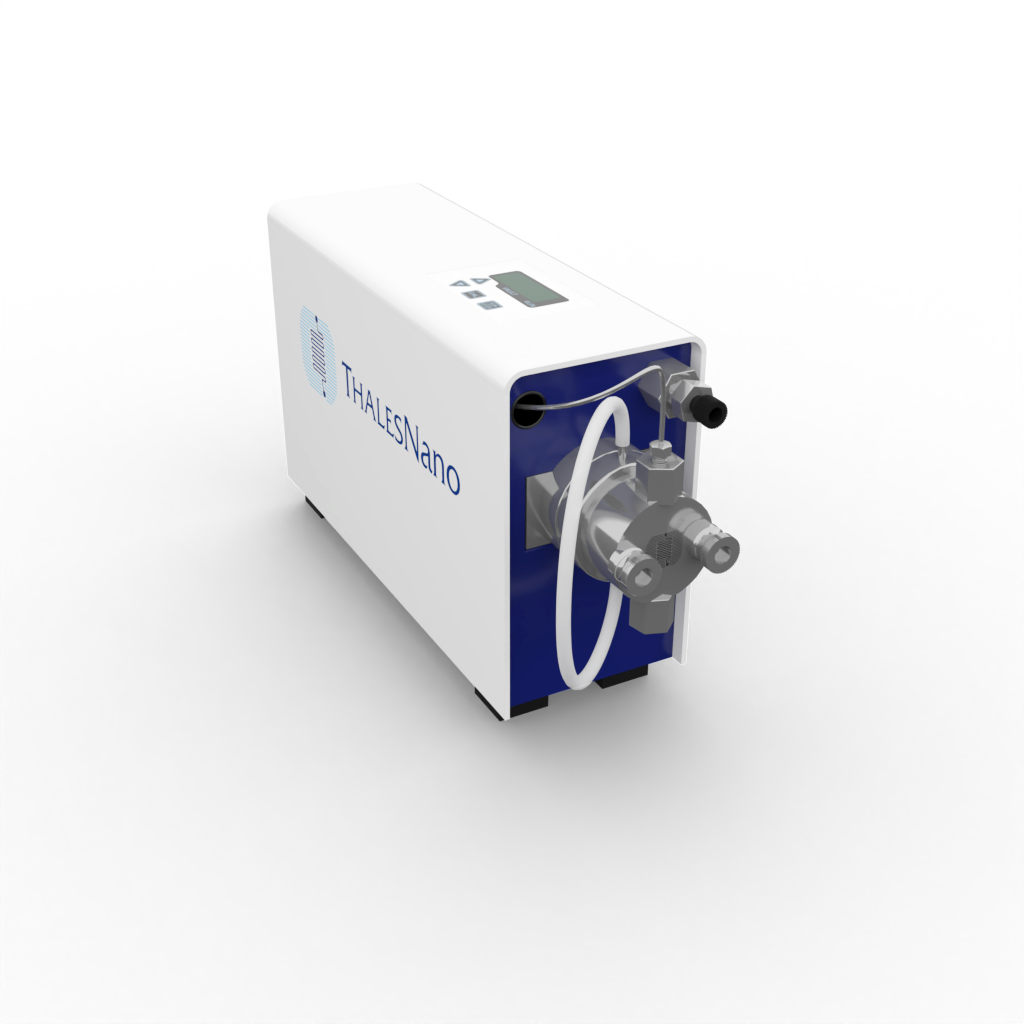
Available heated elements for the Phoenix Flow Reactor
The Phoenix Flow Reactor is a powerful and versatile heating unit capable of reaching temperatures up to 450 °C. A big selection of ready-made reactor setups are available for both homogeneous and heterogeneous applications.
Packed bed reactors: Prefilled CatCarts (30 mm, 70 mm long CatCarts®) and MidiCarts are available for safe and convenient catalyst testing. Moreover, user-fillable metal-metal sealed cartridges with fittings from 1/8” OD to 1/2” OD with 125 mm and 250 mm lengths can be used for a wide range of heterogeneous reactions. The reactor holder sets are made of four pieces in each case; they are required to fill up the internal volume of the Phoenix Flow Reactor's reaction zone.
Loops:
Available in PTFE, Stainless Steel or Hastelloy editions:
- 4, 8, or 16 mL for homogeneous chemistry.
Available in Stainless Steel or Hastelloy editions:
- 40 mL (OD: 1/8", ID: 16 mm)
For custom-sized heated elements please contact us at askthechemist@thalesnano.com.
Applications
Basic configuration:
- SNAr reactions
- Boc-removal
- Claisen rearrangement
- C-alkylation
- N-alkylation
- Supercritical reactions
- Heterocycle synthesis
- Etc.
Addition to basic configuration:
- Hydrogenation
- Oxidation
- Carbonylation
- Etc.
TESTIMONIALS
“Our laboratory specializes in the development, production and test fuels from various feedstock, and ThalesNano’s Phoenix II – H Genie II platform has been a versatile tool for process development, cutting cost in catalyst testing due to its g-kg scalability, and enables safe, in-situ hydrogenation. Aside from that, the system is easy to use and automate, it performs great in a wide variety of experiments.”
FAQ
Do you have more questions?
Reach out to us at any time and experience fast and efficient support tailored to your specific needs.